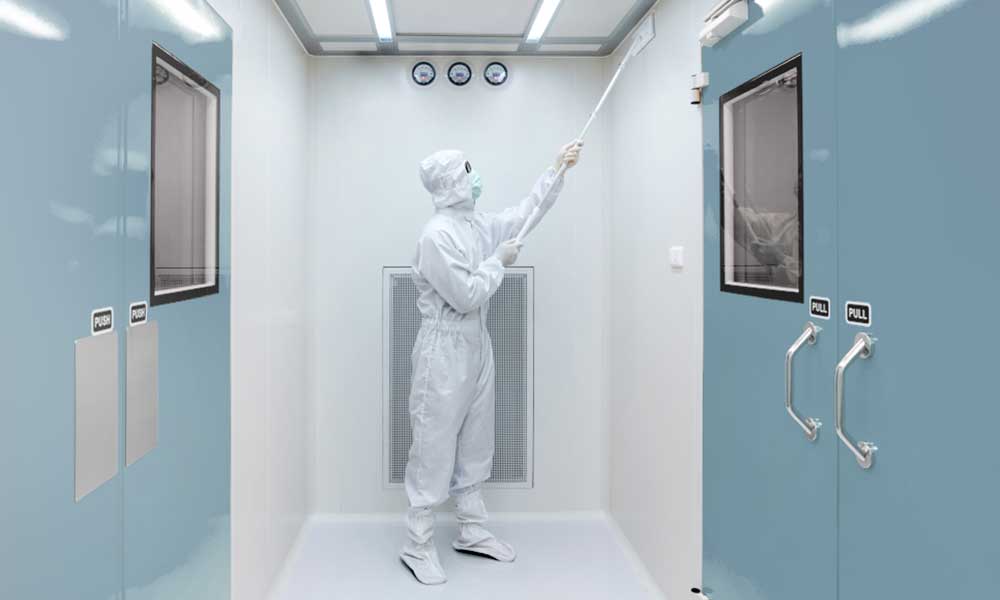
Our Range of Services
for Your "CLEAN" Benefit
From the analysis of your production process up to the
final implementation of your CLEAN solution and beyond, cleanroom.de GmbH is your partner for all required products
around cleanroom technology.
Your Contact:
Markus Thamm
+49 6221 72 87 337
shop@mycleanroom.de
Understanding your production process helps us, to work out and quote customer specific, economic and efficient solutions.
Processing complex new projects around cleanrooms requires time and expert knowledge. The variety of different products and contact persons makes the solutions finding complex.
cleanroom.de GmbH will perform these tasks for you, takes care about scheduling, coordination and administration. From order entry to delivery and installation / acceptance, you have only one contact point with complete cost transparency. cleanroom.de offers you identical pricing as our individual partners would do.
Our Services for Your “CLEAN“ Benefit.
Cleanroom & Components
In microtechnology components and structures become smaller and more sensitive. Particles have as such played a minor roll in the past. Since meanwhile the size of a dust particle surpasses the size of component structures by far, processes under a controlled environment become more and more necessary.
The microtechnology applications are manifold. To be able to work out your best possible solution, it is necessary to internalize and understand your application in detail. This we can assure through our positioning on microtechnology and our experience in this field. Therefore we are able to adapt and work out the cleanroom to your needs and realize a customized, economical and efficient solution.
Factors like temperature and relative humidity are playing an important roll for these solutions. Through our partners we can give answers which are sustainably ensuring the quality of your products.
Welcome to our innovative solution for individually configurable cleanrooms made of fabric - the state of the art in modern cleanroom construction.
Our basic idea is to work with the latest lightweight construction elements made of high-tech materials and fabric to realize cleanrooms quickly, efficiently and cost-effectively. We use feather-light fabric walls with stable outer frames and efficient ventilation systems to build cleanrooms that are second to none.
A fabric separates clean and contaminated air just as reliably as 1 cm thick solid material. However, a cleanroom tent is much more cost-effective, has a shorter production time and lower assembly costs. Nevertheless, it demonstrably fulfills all standards from ISO to GMP.
Our concept allows you to either rent standard cleanrooms according to your needs www.reinraum-mieten.de or purchase them via an installment plan www.reinraum-kaufen.de.
During this rental phase, you can write off the costs directly and carry out extensive tests with the product.
If you would like a customized cleanroom that goes beyond our standard system, we will be happy to prepare an individual offer based on your requirements.
Product life cycles and time to market are getting shorter and shorter. This requires in many cases a flexible production planning. The construction of a complete cleanroom could possibly take too much time and be too expensive. Cleanroom tents offer a good and cost effective solution to meet the increasing need for cleanliness.
A frame can be adjusted to the spatial conditions of your room in all dimensions. Cleanroom curtains which are mounted at the sides of the frame are limiting the clean area. Fan filter units can be mounted on the top or on the side to generate horizontal or vertical air flow. Such a cleanroom tent can even be mounted on casters to offer even more mobility.
Laminar flox boxes are made to create local areas with a high air cleanliness level. This solution is often chosen for assembly or handling processes as well as for storage of components. Laminar flow boxes are mainly used in clean areas but are also frequently used in cleanrooms.
The boxes consist of a housing and a fan filter unit, which supply the working space with clean air. The dimensions can be adjusted to match the respective process. Integration into a production line is easy and flawless.
The base configuration can be set onto any table but options include a base frame with casters or a base frame with drawers.
Fan filter units are used for the generation of clean air. Air is taken in from the top through a fan and pressed through the filter. The circulating air is continuously filtered and provides clean air for the cleanroom. FFU’s are available in standard sizes but can be customized. Pre-filters clean the air before it reaches the main filter and therefore maximize the life time of the more complex main filter.
Different filter types are available. The H14 filter (which is mainly used) features a retention rate of 99.995%. This means that at a particle size of 0.12µm (MPPS=most penetrating particle size), the filter removes at least 99.995% of all particles. At a particle size of 0.3µm, the retention rate is approx. 99.9995%.
Flow rates can easily be adjusted by the use of a potentiometer. Optionally the use of an automatic control system is possible which provides an 8 step control. The control system has different modes like „night reduction“ as well as „MAX“. Through the use of energy efficient EC fans, the power draw is minimized. The noise generation in the workspace is approx. 40 to 52dB (depending on the size), and the models are correspondingly quieter at lower flow velocities.
Cleanroom curtains are a cost-effective alternative to permanently installed cleanroom cabins. The perfect workmanship of the cleanroom curtains meets the high demands made on products for cleanroom technology.
The cleanroom curtain is available as a strip curtain or as a continuous curtain and can be fixed to the wall or ceiling in various ways. The curtains are made of extremely resistant PVC and can be fixed or sliding. The lower edge of the cleanroom curtain can be equipped with a welded lead cord or metal strip. This guarantees an optimal position of the curtain permanently.
Product features:
- Mounting on the wall or the ceiling
- fixed or sliding version
- available as strip curtain or continuous cleanroom curtain
- transparent, extremely resistant material (PVC) in various thicknesses
- Width and length of the curtain or strips made to measure
- antistatic (ESD) or antibacterial finish on request
- flame retardant according to DIN 4102
Garments & Consumables
In order to have an optimal running “system of cleanroom garments” it is necessary that all the individual demands on the cleanroom garments be checked with the requirements of the user at their workstation. Only once this is done the filter between human and product can become effective.
Humans are the biggest source of contamination in the cleanroom. This is the reason why high quality cleanroom garments are absolutely essential for protection of the product.
The following aspects should therefore be considered when choosing garments:
- technical features of the Cleanroom fabric
- wearing comfort and physiological characteristics
- garment construction, e.g. the quality of the seams, the fitting etc.
In order to have an optimal running “system of cleanroom garments” it is necessary that all the individual demands on the cleanroom garments be checked with the requirements of the user at their workstation. Only once this is done the filter between human and product can become effective.
Trust in our competence. Making a decision as to which system gives an optimal solution for your cleanroom is not always easy. For this reason we offer our extensive experience within the field. In order to provide the perfect solution for you, we have devised the following procedures to make the choice of appropriate products easier.
Amongst them are:
- Tests of fabrics under a standardised procedure
- Co-operation with independent institutes to prove our quality standards
- Assembly and continuous development of our own test cleanroom including the ability to test cleanroom products with the use of the Helmke Drum-Method or the modified ASTM F51-68 test methods
- Supply of technical data provided by the manufacturer
- Despatch of samples to our customers for in situ testing
- Complete technical back-up from our in house experts
- Links to a world-wide network of leading cleanroom product manufacturers
This grants our customers complete information for all quoted products, and a high level of confidence whenever an order is placed.
Disposable clothing is often a necessary addition to the textile cleanroom clothing. Depending on the requirements, different designs and qualities must be considered (e.g. antistatic). When handling toxic materials or other hazardous substances, disposable coveralls with sealed seams are used. Efficient protection in the clean room is extremely important, which is why we only work with manufacturers who offer the highest quality and safety for your production processes.
A reduction of contamination can be achieved by the sensible use of different components, if necessary, also with reusable clothing. On request, the disposable clothing is also available sterile - packed individually or as a set. Please do not hesitate to contact us if you have any questions regarding disposable clothing.
As cleanroom gloves are the only garments that commonly come into contact with the product, they have to meet particularly high requirements:
- the abrasion and particle permeability should be as low as possible
- the sense of touch should be kept as sensitive as possible
- the transmission of fingerprints due to sweat and grease must be prevented
Each product has different requirements for the type of glove used. Therefore one cannot assign a glove to all products or processes. So before choosing cleanroom gloves and finger cots, we recommend testing a selection to enable you to choose the glove for your particular requirements.
For the glove user there is often a question mark over the necessity of using disposable gloves, with their associated lower comfort level – if textile gloves would also satisfy the demands of the workplace.
Generally for usage in cleanroom conditions it is always better to choose a powder free, post cleaned glove made from Latex, Nitrile, Vinyl or other synthetic materials such as PE, Neoprene, etc. Only these skin-tight and AQL tested powder free disposable gloves guarantee the necessary protection for your products against contamination caused by human skin.
Where operations and processes require less stringent precautions within cleanrooms then textile gloves may provide the solution. Finally the user has to decide which gloves will meet his requirements.
Cleaning Products
Well thought-out solutions simplify handling and increase user-friendliness. A wide range of available cleanroom accessories allows precise adaptation to every cleaning task.
We offer an extensive range of specialised mops for use in cleanrooms and hygienically sensitive areas. Our high-tech microfibre technologies not only provide excellent cleaning performance but also a very long service life and ensure constant cleanroom suitability.
The testing of our cleanroom mop covers by independent testing institutes guarantees users absolute certainty in terms of conformity and proven cleanroom suitability.
The requirements for mops in cleanroom cleaning are not only very high, but also very different. Tasks range from the sensitive disinfection of sterile GMP cleanrooms to the removal of contaminants such as production residues in technical cleanrooms.
We offer a range of different materials and mop models, each of which is designed and tested for different tasks and different air purity classes.
High-quality accessories are an important component in every cleanroom cleaning system. The aim is to combine cleanroom suitability with ergonomics. The fact that both conformity and the user are at the centre of our developments can be seen in every product.
Well thought-out solutions simplify handling and increase user-friendliness. A wide range of available cleanroom accessories allows precise adaptation to every cleaning task.
Our range of accessories includes mop handles, mop holders and special cleaning systems made of the highest quality stainless steel, plastic and aluminium for all cleanroom classes.
- Telescopic handles or rigid handles (stainless steel / plastic / aluminium)
- Folding mop holder (stainless steel / plastic)
- Special systems for special cleaning (stainless steel / plastic)
An innovative plug-in system enables the handle and attachment to be changed quickly and easily. This not only simplifies handling, but also cleaning and, if necessary, sterilisation of the accessories. All stainless steel accessories and a selection of plastic / aluminium accessories are permanently autoclavable.
The pre-saturation of cleanroom mops is the most advanced method of liquid dosage. Mops do not need to be wrung out in a flat-press, as they are saturated at the beginning of the cleaning procedure. The workflow enables the reliable, quick and easy impregnation of all needed mops.
Save:
- SPACE:> up to 75%
- TIME: > up to 25%
- DESINFECTANT: > up to 50%
Our system enables the strict separation of new and used mops. The construction of the system effectively avoids cross-contamination.
All our materials comply with the regulations of EG GMP and DIN EN ISO. The unit is fully autoclavable and is especially suitable for GMP-cleanrooms and sterile working conditions.
Our cleanroom cleaning trolleys are manufactured according to the highest possible processing standards under all aspects of cleanroom suitability. Their high performance guarantees safe, efficient cleaning processes and high user-friendliness in cleanroom cleaning.
Thanks to the well-thought-out modular principle, our cleaning trolleys can be quickly and easily adapted to all cleaning tasks in the cleanroom. They allow a wide range of equipment and configuration options.
The robust stainless-steel base frames with the stainless-steel tubs fully comply with the requirements of EG GMP and DIN EN ISO 14644. The special surface treatment allows excellent cleanability and is completely autoclavable.
- Suitable for use in all cleanroom areas
- Specially suitable for sterile areas (i.e. medical and pharmaceutical industry)
- Available in different sizes and configurations
- Applicable to various cleaning procedures
In almost every cleanroom, special wipes are used for a variety of applications. When searching for an appropriate wipe you should define which requirements the wipes should fulfill:
- Is the wipe supposed to be for dry or for wet cleaning?
- Should the wipe be especially low in particle emission?
- Should it be a soft wipe, which does not scratch the product?
- Should the wipe be resistant against chemicals?
- Can the surface or the item to be cleaned damage the wipe?
As wipes have many different applications, we offer you a variety of cleanroom wipes made of a number of basic materials, which are produced by varying manufacturing methods. The most important base types are:
- Cotton
- Cellulose
- Polyester/cellulose blend
- Polyester
- Micro fibre
- Polypropylene
- Nylon
- Polyurethane foam, etc.
- Saturated wipes mainly made of polypropylene
Within our standard product range we cover the most common requirements for cleanrooms. In addition, for special cases, we work closely with national and international wipe manufacturers with whom we develop individual customer specific solutions. Their full range is available through us.
Tacky mats prevent the unintentional importation of large quantities of particles into the cleanroom on the soles of people's shoes. The combination of a washable permanent adhesive mat and a strongly adhesive peel off tacky mat offers the optimum protection and reduces the running costs.
Technology
The conditions in a cleanroom need to be verified and qualified repeatedly and continuously. For this tasks several measurement techniques have been established.
Particle counters are used to detect and analyze airborne particles. With a new measurement principle it is now also possible to measure sedimented particles and as such receive an additional value to define the air cleanliness in cleanrooms. More parameters like air speed, temperature, relative humidity, etc. have also have to be checked and recorded on a regular basis.
The use of measuring systems in a holistic concept is dependent on the application and the customer requirements. cleanroom.de GmbH has set up a network of specialists which have done successfully measurement task within cleanrooms over many years.
Particle counters are not only used in industrial research and development but also in clean room technology. The devices suck in a certain amount of air and count out the number of particles using various physical methods.
Various versions are available for different applications and areas of use, which differ in the detectable particle sizes, among other things. The range includes several devices with integrated vacuum pump, display and printer. We would be pleased to submit you an individual offer.
The design of the APMON is an important advantage. It is compact, completely wireless and can be placed very near to (or even on) the working area, for the most accurate measurements. The material is suitable for cleanroom use and is easy to clean.
The design of the APMON is an important advantage. It is compact, completely wireless and can be placed very near to (or even on) the working area, for the most accurate measurements. The material is suitable for cleanroom use and is easy to clean.
The basic system of the APMON consists of one sensor, a base unit and an user friendly user interface. It is possible to add up to 6 sensors per base unit, so multiple locations can be measured at once while it accounts in one clear rapport.
Multifunction devices are used to determine a large number of different measured values in different applications. The applications range from the inspection of ventilation and air conditioning systems, clean room qualification, the creation of air balances, the measurement of process air flows to comfort measurements at workplaces.
Interchangeable probes can be used to record air velocity, temperature, differential pressure and relative humidity.
Standard equipment includes USB cable, software, manual, batteries, carrying case and a calibration certificate. The recommended basic equipment includes a probe for differential pressure measurement, as well as a probe for measuring temperature, air velocity and humidity.
We encounter the dosing of liquids in the most diverse situations: For example, when washing with liquid soap, during adhesive bonding processes or when administering medicine or lubricating plain bearings. Typically, a disturbing dripping or run-off of the medium occurs. Depending on the viscosity, this is sometimes more or sometimes less the case. The reason for this is the pressure reduction on the system and medium side.
The patented cleanValve is a closing valve, which sits directly at the outlet point and seals immediately after dosing. It is implemented as a valve unit that can be integrated into the product and can be used as a component to supplement conventional dosing systems.
Furniture
The clean room products manufactured by us fulfil all of the relevant clean room guidelines. In our production halls we only manufacture product referred equipment. A modern machine park and highly qualified personal guarantee the products for thier highest quality requirements. Leading companies successfully utilize our products in their clean rooms.
The products are used in technical rooms with a high requirement on dust-free work spaces like in the semiconductor, electronics and hard disk industry. The technical design of the products is suitable for the use in ventilated cleanrooms. According to the requirements, horizontal areas can have a normed perforation 10/15 to allow for vertical air flow. The optimal design is supported through the use of stainless steel having a surface with a very fine finish. Furthermore the abrasion resistant surface of the stainless steel warrants that no particles are emitted into the surrounding.
Services
The field of cleanroom services is very diverse. This ranges from training, education, measurements to consulting for your cleanroom planning. The cleaning of clothing but also the cleaning of cleanrooms or cleanrooms themselves are important services that ensure the quality of your cleanroom facilities in the long term.
Production under defined clean room conditions is becoming increasingly important. However, in order to be able to produce in a clean room, some requirements must be met. The parts or assemblies used should be cleaned in accordance with cleanroom requirements before being brought into the cleanroom and adequately packaged before being discharged. For many companies, this necessary process step means tying up own resources or cannot be carried out in-house.
We offer cleanroom-compatible cleaning and packaging of parts and components. The cleaning and packaging of individual parts and assemblies is carried out in a 120 m² clean room, which meets the conditions up to class 5 according to DIN EN ISO 14644-1.
The field of cleanroom services is very diverse. This ranges from training, education, measurements to consulting for your cleanroom planning. The cleaning of clothing but also the cleaning of cleanrooms or cleanrooms themselves are important services that ensure the quality of your cleanroom facilities in the long term.
- Our range of services includes:
- Cleaning of cleanrooms
- Cleaning of components and machines
- Education, Coaching & Training
Cleanroom cleaning and disinfection “Not clean – but pure”
Since 1984, clean room cleaning has been the daily business of our partner. Since they we have continuously developed for the benefit of our customers. In the meantime, more than 150 employees work daily in the cleanrooms of our customers. We know what is important to them and offer them the greatest possible safety, also in revision cleaning. Our quality standards, on which you can rely, stand above everything else.
Cleaning advice
Cleanroom cleaning is not just cleanroom cleaning. For us, the difference begins with our understanding of our customers: We are there for you and listen to you.
You get our know-how, our commitment and an individual cleaning concept. We optimize your cleaning processes and, if you wish, we can take over the planning of cleanrooms together with our proven partners.
- Individual hygiene concepts
- Optimization of the cleaning processes
- Training concepts for your employees
Revision Cleaning
Cleaning a clean room is a special challenge, especially after a construction project. Dust and particles pollute the room and from the first day of operation all legal regulations of the respective clean room class must be meticulously observed. We work according to DIN ISO 14644-4/ VDI 2083 sheet 4 and take into account all individual conditions that are decisive in your daily work.
- Fast, on-schedule implementation
- Compliance with all legal requirements
- Guaranteed quality standards
Cleanroom cleaning and disinfection
You work and we clean. Nowhere is constant cleaning as essential as in clean rooms during operation. We know what is important to you and work according to DIN ISO 14644-5 / VDI 2083- 5.1. man and material have only one goal with us: maximum safety for you. It goes without saying that we prove the quality and particle measurement. Complete GMP and DIN-compliant documentation is part of our standard.
- Proof of quality and particle measurement
- Optimized cleaning processes
- Complete, GMP and DIN-compliant documentation
Cleaning of components and machines
Production under strict clean room conditions is becoming increasingly important. In order to be able to produce in a clean room, however, a number of requirements must be met. Depending on the area of application, parts or assemblies must be cleanroom-cleaned before being brought into the cleanroom and then adequately packaged before they can be disposed of. For many companies, this necessary process step means that internal precautions must be taken or cannot be carried out in-house.
We offer cleanroom compatible cleaning and packaging of parts and components. The cleaning and packaging of individual parts and assemblies is carried out in a 120 m² clean room, which meets the requirements up to class 5 according to DIN EN ISO 14644-1.
Our company is specialized in services which meet the highest requirements in hygiene and dust-free preparation of cleanroom garments. Our certified cleanroom operations allow professional decontamination for garments of all cleanroom classes, especially for pharma classes A - D and ISO-classes.
With our partner having over 25 years of experience in laundry services for cleanroom garments and professional decontamination of apparels, we offer full-service leasing concepts - including stockkeeping of garments, barcode tracking system and support in quality management.
We ensure that you are provided with decontaminated or sterilized cleanroom garments of highest-quality on time. Product handling is tailored to your specific requirements. Our professional pick-up and delivery service is performed direct and individual. The contaminated garment will be picked-up weekly or bi-weekly on the agreed day. The handling and delivery generally takes one week. All cleanroom garments are transported in special boxes, which are cleaned after each use. With our tracking system, we ensure that both the defined cycles are maintained as well as that the whereabouts of the cleanroom garments are known at all times.
Besides measurements for cleanroom certification and recertification according to VDI 2083 and ISO 14644, we also offer measurements for cleanroom and cleanliness suitability.
According to the standard, measurements for certification include the following points:
- Visual inspection
- Differential pressure measurement between adjacent areas
- Filter tightness measurement
- Filter integrity test / leakage test
- Outflow velocity at the HEPA/ULPA filter / volume flow determination
- Temperature measurement
- Humidity measurement
- Determination of the air purity class
- Measurement of particles on surfaces (qualitative)
- Recovery time measurement / recovery test
- Flow visualization
- Lighting measurement
- Noise measurement
After completion you will receive a detailed protocol with a graphical representation of the results.
The access to a clean room is trained. The order of the dressing procedure is trained. In a given order with display of the next steps the entering of the cleanroom is trained practically. Subsequently, a dressing procedure is carried out without instructions. If all steps have been carried out correctly and consistently, the participant is given access to the clean room with simultaneous indication of successful completion. The personal data is stored and printed out in order to document the results for audit purposes.
Consulting & Training
cleanroom.de GmbH specialises in supporting small and medium-sized companies in planning and implementing individual cleanroom systems. The goal of creating efficient and economical solutions, providing customers with comprehensive advice and sustainable supply is consistently pursued.
As the need to manufacture products under clean conditions is growing, more and more organizations are faced with the task of investing in cleanroom technology. There are many different tasks to be solved and the questions are manifold.
The handling of complex new projects around the cleanroom requires time and expert knowledge. The multitude of different products and contact persons makes finding a solution complicated. Understanding your production process helps us to develop and offer customer-oriented, cost-optimized and efficient solutions.
Together with our partners, we can therefore propose complete cleanroom solutions and advise you on the tasks involved.
Based on many years of experience in working in cleanrooms and cleanroom environments, we offer coaching and training on cleanroom-specific topics.
In-house coaching for cleaning and behaviour
Our coaching sessions provide you with targeted and practice-oriented support in qualifying your employees for working under cleanroom conditions. You define a daily goal - and we put together a coaching package tailored to your company. In addition, the standardised in-house trainings are available in the following 3 formats:
Training Cleanroom Behaviour
The training includes, among other things, the basics of cleanroom technology, factors influencing cleanliness, behavioral and awareness training, and the dressing procedure for cleanroom overalls.
Training Cleanroom Cleaning
This training concentrates on the most important theoretical basics and imparts them practically and with many tips. From the basics of cleanroom cleaning to wiping techniques, documentation and control.
Training cleanroom behaviour and cleaning
This training combines the requirements from behaviour and cleaning and allows an individual consideration in your cleanroom operation
Training course cleanroom manager:
We are happy to give you the opportunity to take part in the special and certified training course for certified cleanroom managers at the Cleanroom Future Campus.
In 6 modules the participants will receive a clear structure for processes, quality, management and efficiency to manage and optimize your friction room operation.